Industrial Process Analysis and Remote Final Acceptance Testing
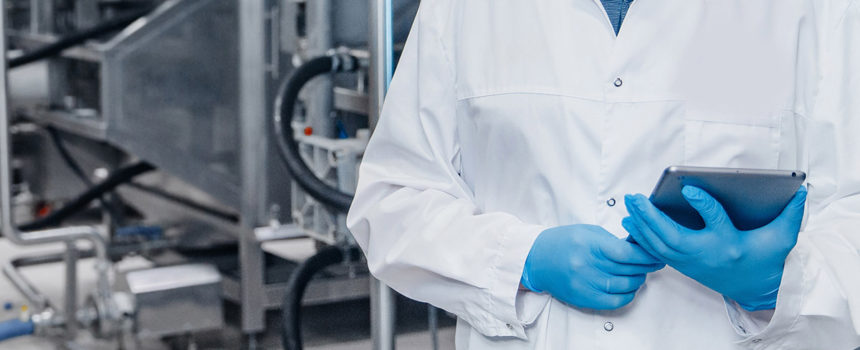
The coronavirus (COVID-19) pandemic brought about unprecedented challenges for businesses worldwide, disrupting operations and limiting face-to-face interactions. As MSA Safety’s process analysis experts, we responded to these challenges with innovation and flexibility, demonstrating our ability to adapt and evolve in the face of adversity. For this success story, MSA Safety was able to leverage remote video conferencing tools to facilitate live, real-time interaction for a prescription medical equipment manufacturer. We’re proud to have implemented solutions that have enabled us to continue serving our customers and maintaining high standards of quality and safety.
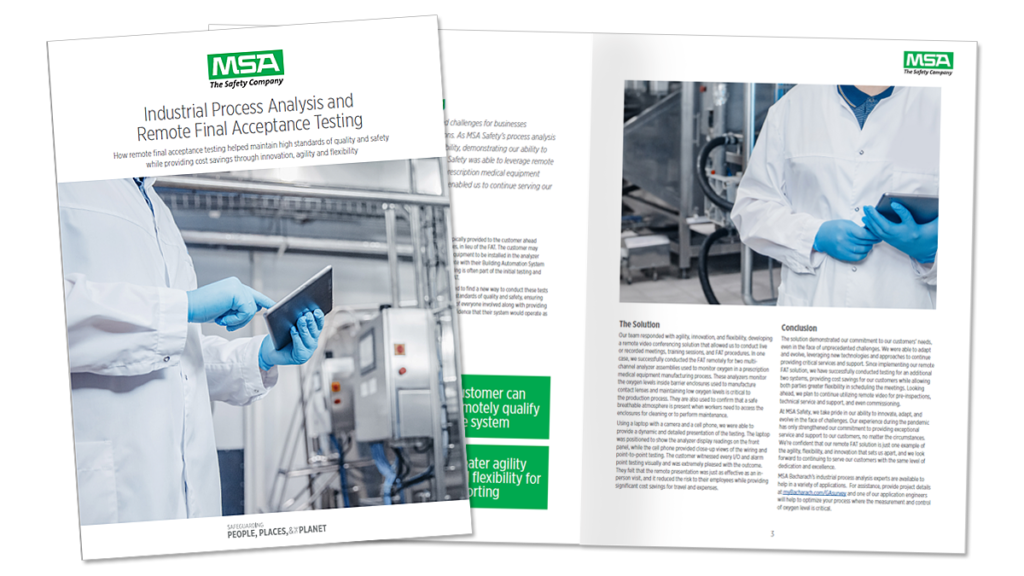
Download your copy of this success story and find out how MSA Safety’s gas inerting experts can help you to remotely qualify your system and provide cost savings for reduced travel and expenses.
When the pandemic first hit, we prioritized the health and safety of our employees, customers, and partners. Our company policies prohibited in-person contact with anyone, and social distancing measures were mandated for all personnel required to be on-site. However, we recognized that many of our customers still required critical services and support, and we sought to find new and innovative ways to meet their needs.
Typically, for larger plant-integrated systems where Final Acceptance Testing (FAT) is required, the customer would send a representative to inspect and witness the verification testing in person especially where there are individual calibration and testing procedures for the subassemblies that are performed before final assembly. A final system test is generally performed by Production, along with an inspection carried out by Quality Control to ensure the product meets design and performance specifications.
These documents are typically provided to the customer ahead of time, and in some cases, in lieu of the FAT. The customer may also provide additional equipment to be installed in the analyzer enclosures to communicate with their Building Automation System (BAS). Point-to-Point wiring is often part of the initial testing and verification prior to the FAT.
We realized that we needed to find a new way to conduct these tests that would meet our high standards of quality and safety, ensuring the health and well-being of everyone involved along with providing the customer with the confidence that their system would operate as planned.
Solution
Our team responded with agility, innovation, and flexibility, developing a remote video conferencing solution that allowed us to conduct live or recorded meetings, training sessions, and FAT procedures. In one case, we successfully conducted the FAT remotely for two multichannel analyzer assemblies used to monitor oxygen in a prescription medical equipment manufacturing process. These analyzers monitor the oxygen levels inside barrier enclosures used to manufacture contact lenses and maintaining low oxygen levels is critical to the production process. They are also used to confirm that a safe breathable atmosphere is present when workers need to access the enclosures for cleaning or to perform maintenance.
Using a laptop with a camera and a cell phone, we were able to provide a dynamic and detailed presentation of the testing. The laptop was positioned to show the analyzer display readings on the front panel, while the cell phone provided close-up views of the wiring and point-to-point testing. The customer witnessed every I/O and alarm point testing visually and was extremely pleased with the outcome. They felt that the remote presentation was just as effective as an in-person visit, and it reduced the risk to their employees while providing significant cost savings for travel and expenses.
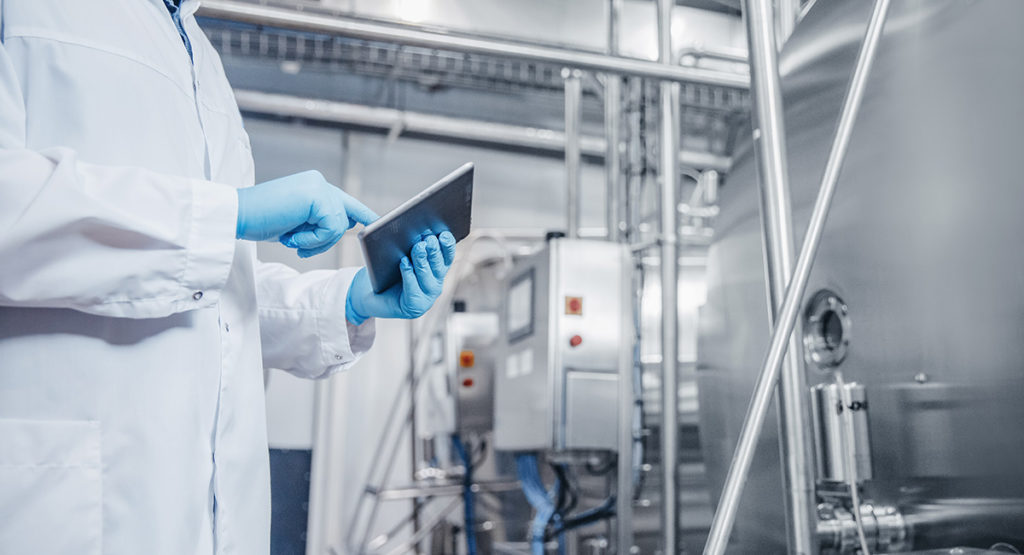
Conclusion
The solution demonstrated our commitment to our customers’ needs, even in the face of unprecedented challenges. We were able to adapt and evolve, leveraging new technologies and approaches to continue providing critical services and support. Since implementing our remote FAT solution, we have successfully conducted testing for an additional two systems, providing cost savings for our customers while allowing both parties greater flexibility in scheduling the meetings. Looking ahead, we plan to continue utilizing remote video for pre-inspections, technical service and support, and even commissioning.
At MSA Safety, we take pride in our ability to innovate, adapt, and evolve in the face of challenges. Our experience during the pandemic has only strengthened our commitment to providing exceptional service and support to our customers, no matter the circumstances. We’re confident that our remote FAT solution is just one example of the agility, flexibility, and innovation that sets us apart, and we look forward to continuing to serve our customers with the same level of dedication and excellence.
MSA Bacharach’s industrial process analysis experts are available to help in a variety of applications. For assistance, provide project details at myBacharach.com/GAsurvey and one of our application engineers will help to optimize your process where the measurement and control of oxygen level is critical.